Характеристики стали 52Н
Сталь 52Н относится к классу конструкционных рессорно-пружинных сталей повышенной прочности, регламентируемых ГОСТ 14959-2016. Её химический состав оптимизирован для достижения исключительных упругих свойств:
- Никель (1.4-1.8%) - повышает прокаливаемость и вязкость, снижая порог хладноломкости до -60°C.
- Хром (0.7-1.0%) - усиливает эффект дисперсионного твердения при отпуске, повышая предел упругости.
- Кремний (0.17-0.37%) - улучшает сопротивление малым пластическим деформациям, критически важное для пружинных применений.
- Углерод (0.49-0.56%) - обеспечивает высокую прочность после термообработки за счёт образования мартенсита.
Физико-механические свойства после оптимальной термообработки:
Параметр | Значение |
---|---|
Предел прочности (σв) | 1500-1700 МПа |
Предел текучести (σ0.2) | 1300-1450 МПа |
Относительное удлинение (δ) | 9-11% |
Ударная вязкость (KCU) | 60-80 Дж/см² |
Твердость (HRC) | 44-48 |
Температурные характеристики:
- Рабочий диапазон: от -60°C до +250°C (сохранение упругих свойств).
- Критическая точка Ac1: 730°C (начало образования аустенита при нагреве).
- Температура отпуска: 280-320°C (оптимальное сочетание прочности и пластичности).
Термическая обработка
Для достижения оптимального комплекса механических свойств сталь 52Н подвергается многоступенчатой термообработке:
Этап | Параметры | Микроструктура |
---|---|---|
Отжиг | 780-800°C, охлаждение с печью 20°C/ч до 600°C | Сорбитообразный перлит |
Закалка | 850-870°C, охлаждение в масле | Мартенсит с остаточным аустенитом (5-8%) |
Отпуск | 300-350°C, выдержка 2 часа | Троостит отпуска |
Критическая скорость охлаждения при закалке составляет 50-70°C/с, что требует использования минеральных масел марки И-20 или их аналогов. Для деталей сложной формы рекомендуется ступенчатая закалка с выдержкой при 300-350°C для снижения термических напряжений.
Формула расчета прокаливаемости по диаметру:
Dидеал = K·(0.54·%C + 0.16·%Si + 0.19·%Mn + 0.13·%Cr + 0.18·%Ni)
где K = 1.5 для масляной закалки. Для 52Н Dидеал ≈ 25-30 мм.
Интересный факт: при закалке с 870°C в стали 52Н образуется около 7% остаточного аустенита, который постепенно превращается в мартенсит при эксплуатации, создавая эффект "самоподкачки" пружин.
Применение
Благодаря уникальному сочетанию прочности и пластичности сталь 52Н широко используется в ответственных узлах:
- Автомобильные рессоры и пружины подвески - выдерживают до 500 тысяч циклов нагружения.
- Авиационные амортизаторы - работоспособны при температурах от -60°C до +150°C.
- Пружины клапанов ДВС - сохраняют свойства при длительном воздействии вибрации.
- Измерительные приборы (тензодатчики, мембраны) - обеспечивают стабильность показаний.
- Буровое оборудование - устойчивы к ударным нагрузкам в агрессивных средах.
Сравнительные характеристики с аналогами:
Марка | σв, МПа | δ, % | KCU, Дж/см² | Стоимость |
---|---|---|---|---|
52Н | 1500-1700 | 9-11 | 60-80 | Высокая |
60С2А | 1400-1600 | 6-8 | 30-50 | Средняя |
65Г | 1300-1500 | 5-7 | 20-40 | Низкая |
Формула расчета напряжения в пружине:
τ = (8·F·D)/(π·d³)
где:
F - приложенная сила (Н),
D - средний диаметр витка (мм),
d - диаметр проволоки (мм).
Сварка и обработка
Особенности технологической обработки стали 52Н:
- Механическая обработка: рекомендуется в отожжённом состоянии (HB 207-229). Скорость резания 50-70 м/мин, подача 0.1-0.15 мм/об.
- Шлифование: электрокорундовые круги зернистостью 40-60, охлаждение эмульсией.
- Сварка: требует предварительного подогрева до 250-300°C. Оптимально - аргонодуговая сварка с проволокой Св-10ХГСМФ.
- Поверхностное упрочнение: дробеструйная обработка повышает предел выносливости на 20-25%.
Интересный факт: пружины из стали 52Н после дробеструйной обработки выдерживают на 30% больше циклов нагружения благодаря созданию сжимающих остаточных напряжений в поверхностном слое.
Влияние обработки на свойства:
Метод обработки | Предел выносливости, МПа | Кол-во циклов до разрушения |
---|---|---|
Без обработки | 600-650 | 2×106 |
Дробеструйная | 750-800 | 3×106 |
Азотирование | 900-950 | 5×106 |
Популярные вопросы
Чем отличается сталь 52Н от 50НХС?
Основное отличие заключается в содержании легирующих элементов: 52Н содержит 1.4-1.8% никеля и 0.7-1.0% хрома, тогда как 50НХС имеет 4.5-5.5% никеля и 0.8-1.2% хрома. Более высокое содержание никеля в 50НХС обеспечивает лучшую прокаливаемость и ударную вязкость при низких температурах. Однако 52Н превосходит по пределу упругости (1300-1450 МПа против 1200-1350 МПа у 50НХС), что делает её предпочтительной для пружин с высокими требованиями к точности.
Какие аналоги 52Н существуют в международных стандартах?
Ближайшие зарубежные аналоги включают AISI 5150 (США), 55Cr3 (Европа), SUP9 (Япония). Американский аналог AISI 5150 имеет схожий химический состав, но несколько меньшее содержание никеля (0.7-1.0%). Европейская сталь 55Cr3 содержит больше хрома (0.9-1.2%) при отсутствии никеля. Российская 52Н выигрывает по комплексному сочетанию свойств благодаря оптимальному балансу никеля и хрома, что обеспечивает лучшую стабильность упругих характеристик.
Как правильно выбрать режим отпуска для пружин из 52Н?
Оптимальный режим отпуска зависит от требуемого сочетания прочности и пластичности. Для большинства пружинных применений рекомендуют отпуск при 300-350°C в течение 2 часов - это обеспечивает твердость 44-48 HRC при сохранении достаточной вязкости. Для ответственных пружин с повышенными требованиями к стабильности свойств применяют двухступенчатый отпуск: сначала 250°C (1 час), затем 350°C (1 час). Критически важно медленное охлаждение после отпуска (в печи) для предотвращения отпускной хрупкости.
Можно ли использовать 52Н для изготовления рессор грузовых автомобилей?
Да, сталь 52Н широко применяется для изготовления рессор грузовых автомобилей средней грузоподъемности (до 10 тонн). Для тяжелых грузовиков (свыше 15 тонн) предпочтительнее стали с более высоким содержанием кремния (60С2А, 65С2ВА). Рессоры из 52Н выдерживают до 500 тысяч циклов нагружения при правильной термообработке и дробеструйной обработке. Важно учитывать, что максимальная рабочая температура не должна превышать 250°C, иначе начинается разупрочнение из-за коагуляции карбидов.
Каковы особенности сварки стали 52Н?
Сварка 52Н требует специальных технологий из-за склонности к образованию закалочных структур. Рекомендуется предварительный подогрев до 250-300°C и последующая термообработка. Наилучшие результаты дает аргонодуговая сварка с присадочной проволокой Св-10ХГСМФ. После сварки обязателен высокий отпуск при 600-650°C для снятия напряжений. Для ответственных конструкций предпочтительнее использовать контактную сварку или механические соединения (болты, заклепки).
Интересные факты
- Сталь 52Н использовалась в конструкции подвески первых советских луноходов, выдерживая перепады температур от -150°C до +150°C.
- Пружины из 52Н в механических часах могут сохранять точность хода до 50 лет благодаря минимальной релаксации.
- При специальной обработке предел выносливости 52Н достигает 800 МПа - это рекорд для сталей данного класса.
- В авиации пружины из 52Н выдерживают до 10 миллионов циклов нагружения без разрушения.
- На базе 52Н разработаны специальные сплавы для 3D-печати методом селективного лазерного спекания.
Купить сталь марки 52Н от поставщика
металлургической продукции ООО «НПО ЛМК»
Купить сталь необходимой Вам марки в Челябинске можно несколькими способами:
- Позвонить по телефону +7 (800) 511-03-97
- Написать на почту: chel@npolmk.ru
- Оформить заявку на сайте
- Приехать по адресу: 454091, г. Челябинск, ул. Пушкина, д. 71
Перед поставкой, вся сталь проходит контроль на соответствие нормативным стандартам. Вместе с заказом Вы получите сопроводительные документы и технические карты.
Наши специалисты всегда готовы проконсультировать Вас по особенностям и свойствам различных марок и подсказать подходит ли та или иная марка для Ваших целей.
Подпишитесь на нашу рассылку
Хотите оставаться в курсе интересных событий? Введите адрес электронной почты и первыми узнавайте об акциях и спецпредложениях.
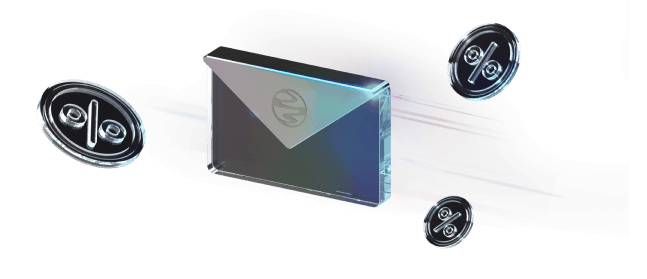