52К13Ф в Челябинске
Название товара | Краткое описание |
---|---|
Магнитно твердый сплав 52К13Ф ГОСТ 10994-74 в слитках |
Характеристики стали 52К13Ф
Сталь 52К13Ф относится к высоколегированным хромистым сталям мартенситного класса, разработанным для работы в условиях абразивного износа и ударных нагрузок. Её химический состав регламентируется ГОСТ 5632-2014:
- Углерод (0.45-0.55%) - обеспечивает высокую твёрдость после закалки (формирует карбиды хрома и ванадия).
- Хром (12.0-14.0%) - создаёт устойчивую пассивирующую плёнку, повышая коррозионную стойкость в окислительных средах.
- Ванадий (0.8-1.2%) - образует мелкодисперсные карбиды VC, повышающие износостойкость и красностойкость.
- Кремний (0.8-1.2%) - усиливает окалиностойкость и упругие свойства материала.
Физико-механические свойства после оптимальной термообработки:
Параметр | Значение |
---|---|
Предел прочности (σв) | 1600-1800 МПа |
Твёрдость (HRC) | 56-60 |
Ударная вязкость (KCU) | 30-40 Дж/см² |
Модуль упругости (E) | 215 ГПа |
Коэффициент теплопроводности | 28 Вт/(м·К) |
Коррозионная стойкость в различных средах:
- Атмосферные условия: скорость коррозии 0.01-0.03 мм/год (в 8-10 раз ниже, чем у углеродистых сталей).
- Морская вода: устойчива к точечной коррозии при содержании хлоридов до 500 мг/л.
- Кислотные среды: сохраняет стойкость в 10% HNO3 при температуре до 50°C.
Термическая обработка
Для достижения оптимального комплекса свойств сталь 52К13Ф подвергается многоступенчатой термообработке:
Операция | Режим | Микроструктура |
---|---|---|
Отжиг | 850-870°C, охлаждение с печью 30°C/ч до 600°C | Сорбитообразный перлит + карбиды |
Закалка | 1000-1020°C, охлаждение в масле или воздушной струе | Мартенсит с остаточным аустенитом (12-15%) |
Отпуск | 200-250°C, выдержка 2-3 часа | Закалённый мартенсит + дисперсные карбиды |
Критические точки фазовых превращений:
- Ac1 = 820-840°C (начало образования аустенита)
- Ac3 = 950-970°C (окончание аустенитизации)
- Ms = 220-240°C (начало мартенситного превращения)
Формула расчёта эквивалента карбидообразования (CEV):
CEV = %C + %V/5 + %Cr/8
Для 52К13Ф CEV ≈ 1.2-1.4, что указывает на высокую склонность к карбидообразованию.
Интересный факт: при закалке с 1020°C в стали сохраняется до 15% остаточного аустенита, который постепенно превращается в мартенсит при эксплуатации под нагрузкой - это обеспечивает эффект самоподкалки.
Применение
Благодаря уникальному сочетанию износостойкости и ударной вязкости сталь 52К13Ф широко используется в следующих областях:
- Горнодобывающее оборудование (зубья ковшей экскаваторов, дробящие плиты) - ресурс в 3-5 раз выше, чем у сталей 110Г13Л.
- Нефтегазовая промышленность (клапаны буровых насосов, направляющие аппараты) - стойкость к эрозии при содержании абразива до 15%.
- Цементное производство (лопатки вентиляторов, сепараторы) - устойчивость к абразивному износу при температурах до 400°C.
- Пищевая промышленность (ножи для резки замороженных продуктов) - сохраняет остроту кромки в 4-6 раз дольше обычных сталей.
Сравнительные характеристики износостойкости:
Материал | Относительная износостойкость | Ударная вязкость (Дж/см²) |
---|---|---|
52К13Ф | 1.0 (база) | 35-40 |
110Г13Л | 0.6-0.7 | 80-100 |
Х12МФ | 1.2-1.3 | 20-25 |
У10А | 0.3-0.4 | 15-20 |
Формула расчёта ресурса детали при абразивном износе:
T = (K·HV²)/(ρ·v·P)
где:
K - коэффициент износостойкости (0.8-1.2 для 52К13Ф),
HV - твёрдость по Виккерсу,
ρ - концентрация абразива,
v - скорость относительного движения,
P - контактное давление.
Сварка и обработка
Особенности технологической обработки стали 52К13Ф:
- Механическая обработка: рекомендуется выполнять в отожжённом состоянии (HRC 22-25) с применением твёрдосплавного инструмента. Скорость резания 40-60 м/мин, подача 0.1-0.2 мм/об.
- Шлифование: используют электрокорундовые круги зернистостью 40-60 на керамической связке. Во избежание прижогов применяют обильное охлаждение.
- Сварка: требует предварительного подогрева до 300-350°C и последующего отпуска. Оптимально - аргонодуговая сварка с проволокой Св-10Х17Т. Предел прочности сварного шва достигает 90% от основного металла.
- Поверхностное упрочнение: азотирование (толщина слоя 0.2-0.3 мм, твёрдость 1100-1200 HV) или лазерная закалка (глубина 0.8-1.2 мм, твёрдость 62-64 HRC).
Интересный факт: при азотировании 52К13Ф образуется слой ε-нитрида хрома CrN с микротвёрдостью до 1800 HV, что делает его одним из самых износостойких материалов для пар трения.
Сравнение методов упрочнения:
Метод | Глубина слоя, мм | Твёрдость | Температура обработки |
---|---|---|---|
Объёмная закалка | На всю толщину | 58-60 HRC | 1000-1020°C |
Азотирование | 0.2-0.3 | 1100-1200 HV | 500-520°C |
Лазерная закалка | 0.8-1.2 | 62-64 HRC | Локальный нагрев |
Популярные вопросы
Чем отличается 52К13Ф от аналогичных сталей типа Х12МФ?
Основное отличие заключается в повышенном содержании хрома (12-14% против 11-12.5% у Х12МФ) и наличии ванадия (0.8-1.2%), что обеспечивает 52К13Ф лучшую коррозионную стойкость в окислительных средах. Микроструктура 52К13Ф содержит более мелкие и равномерно распределённые карбиды благодаря ванадию, что повышает сопротивление абразивному износу на 15-20%. Однако Х12МФ превосходит по красностойкости за счёт молибдена, что важно для режущего инструмента.
Какие аналоги 52К13Ф существуют в международных стандартах?
Ближайшие зарубежные аналоги включают AISI 440C (США), 1.4125 (Германия), SUS440C (Япония). Европейская сталь 1.4125 имеет практически идентичный химический состав, но более жёсткие допуски по примесям. Американский аналог AISI 440C содержит больше углерода (0.95-1.2%), что повышает твёрдость до 60-62 HRC, но снижает ударную вязкость. Российская 52К13Ф выигрывает по балансу свойств благодаря оптимальному соотношению хрома и ванадия.
Как правильно выбрать режим отпуска для 52К13Ф?
Оптимальный режим отпуска зависит от требуемого сочетания твёрдости и вязкости. Для большинства применений рекомендуют двухступенчатый отпуск: сначала при 200-220°C для снятия напряжений, затем при 300-320°C для стабилизации структуры. Общая длительность процесса 3-4 часа с медленным охлаждением (30-50°C/ч). При повышенных требованиях к ударной вязкости применяют отпуск при 400-450°C, снижая твёрдость до 50-52 HRC, но увеличивая KCU в 1.5-2 раза.
Каков ресурс деталей из 52К13Ф в условиях абразивного износа?
Ресурс зависит от условий эксплуатации: при работе с кварцевым песком (размер частиц 0.1-0.3 мм, концентрация 10%) типичный срок службы составляет 800-1200 часов до критического износа. В более мягких условиях (глина, мелкодисперсные шламы) ресурс может достигать 3000-5000 часов. Поверхностное упрочнение (азотирование, лазерная закалка) увеличивает износостойкость в 1.5-3 раза. Важно учитывать, что при температурах выше 450°C начинается интенсивное разупрочнение из-за коагуляции карбидов.
Можно ли использовать 52К13Ф для изготовления режущего инструмента?
Да, 52К13Ф применяется для изготовления специализированного режущего инструмента, работающего в агрессивных средах: ножей для резки картона с минеральными наполнителями, дисковых фрез по стеклопластикам, свёрл по алюминиевым сплавам с кремнием. Однако для универсального инструмента предпочтительнее стали с более высоким содержанием углерода и молибдена (Р6М5, Х12МФ). Оптимальная геометрия режущей кромки для 52К13Ф: передний угол 8-12°, задний угол 10-15°, радиус закругления 15-20 мкм.
Интересные факты
- Сталь 52К13Ф использовалась при создании первых советских буровых долот для сверхглубоких скважин, выдерживая давление до 1000 атмосфер.
- При специальной обработке поверхность 52К13Ф может достигать шероховатости Ra 0.02 мкм, что сравнимо с оптическим стеклом.
- В составе Международной космической станции есть узлы из 52К13Ф, работающие в условиях космического вакуума.
- Меч, выкованный из 52К13Ф с многослойной термообработкой, способен разрубать стальные прутья диаметром 10 мм без повреждения кромки.
- На базе 52К13Ф разработаны специальные сплавы для 3D-печати методом селективного лазерного спекания (SLM).
Купить сталь марки 52К13Ф от поставщика
металлургической продукции ООО «НПО ЛМК»
Купить сталь необходимой Вам марки в Челябинске можно несколькими способами:
- Позвонить по телефону +7 (800) 511-03-97
- Написать на почту: chel@npolmk.ru
- Оформить заявку на сайте
- Приехать по адресу: 454091, г. Челябинск, ул. Пушкина, д. 71
Перед поставкой, вся сталь проходит контроль на соответствие нормативным стандартам. Вместе с заказом Вы получите сопроводительные документы и технические карты.
Наши специалисты всегда готовы проконсультировать Вас по особенностям и свойствам различных марок и подсказать подходит ли та или иная марка для Ваших целей.
Подпишитесь на нашу рассылку
Хотите оставаться в курсе интересных событий? Введите адрес электронной почты и первыми узнавайте об акциях и спецпредложениях.
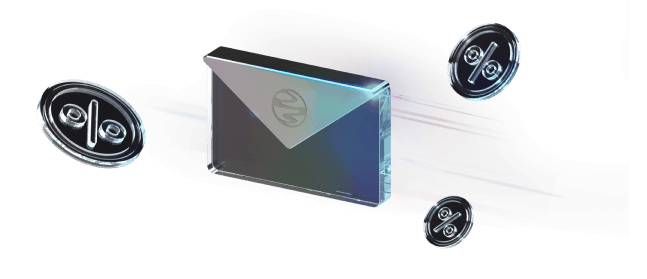